On May 10 this year, we described the ongoing collaboration with our partner Schlötter, who are specialists in developing and selling chemical electrolytes for electroplating. This collaboration has gone very well, and we have now succeeded in completing all three chemical baths needed to manufacture JIRS30, our in-house-developed sensor element.
When we decided to switch to “full fabless,” i.e., where JonDeTech outsources the entire production process but still owns the product design and sets the requirements, the company established a cooperation agreement with the chemical specialist Schlötter. After just over a year of collaboration, it is gratifying to inform you that we have now completed (industrialized) the three different chemical mixtures as well as the required analysis methods. See the picture below.
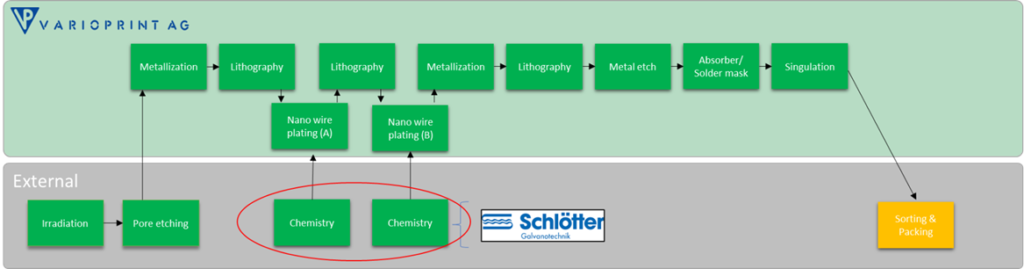
Being able to fill the holes created during ion irradiation and pore etching with two different metals via three different chemical baths are some of the most critical process steps in the production of JonDeTech’s JIRS30 sensor element. Until the collaboration with Schlötter, JonDeTech used self-developed chemical baths without the support of any advanced analysis methods. When we took the step to industrialize this process, we have, through the collaboration with Schlötter, gained a significantly deeper understanding of all the constituent parts. This has created completely new conditions for us to continuously challenge and improve these processes.
In doing so, we have succeeded, among other things, in;
- Simplifying the pretreatment.
- Improving the quality of copper layers.
- Reduce process time for metal A by approximately 40 percent.
- Reduce process time for metal B by approximately 75 percent.
Through the implemented analysis method, we can also optimize the lifespan of our baths, something that was not possible before. Since chemicals are both expensive to buy and to destroy, this work gives us very good opportunities to reduce both production costs and environmental impact.
With the stability we have now achieved in the chemical baths, we have eliminated one of the variations that historically made it difficult, if not impossible, to create predictability in the process flow. In combination with the brand-new industrial electroplating line (WED line), we now have the right conditions for quality assurance of the nanowires that constitute the foundation of our unique sensor element.